5S: Simple Steps, Powerful Impact
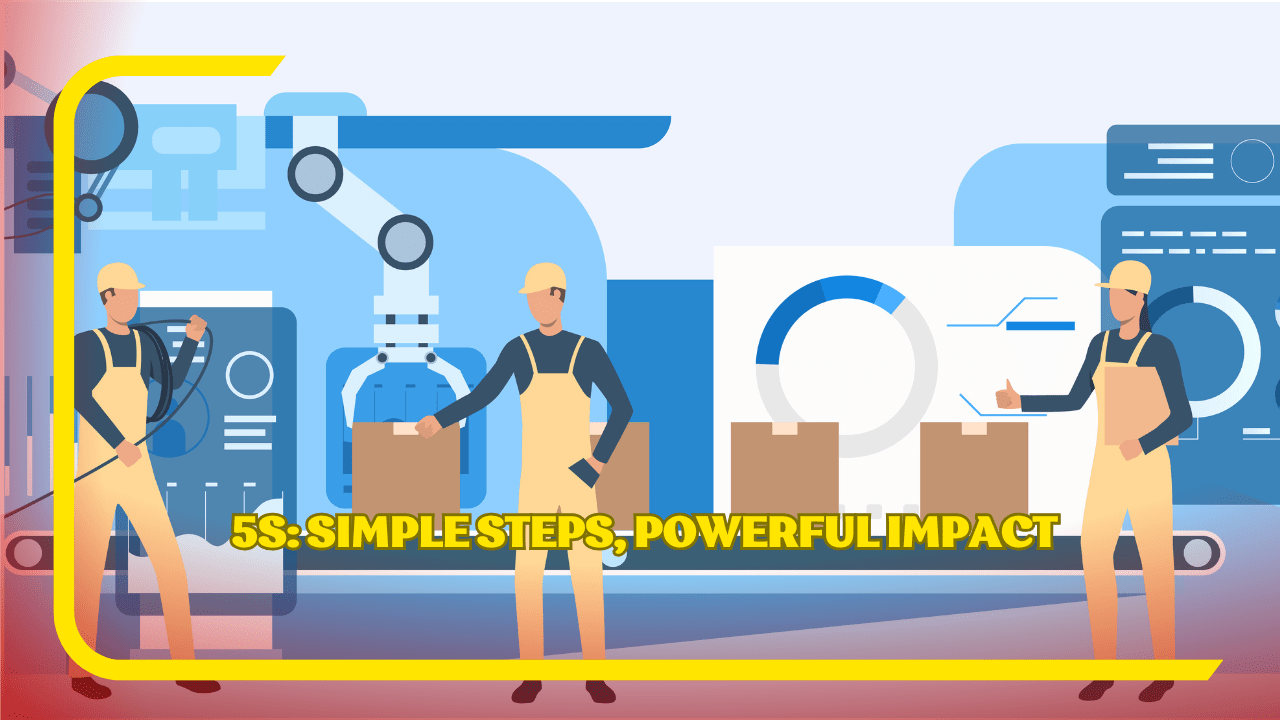
5S: Simple Steps, Powerful Impact
In today’s rapidly evolving world, the 5S methodology has become an essential aspect of workplace organization and operational efficiency across industries. A Business Process Improvement Consultant can help companies apply this methodology to streamline operations and maximize productivity. 5S developed in Japan in the 90s in the 1960s by Hiroyuki Hirano. The term 5S comes from 5 Japanese words that represent the core principles of workplace organization and standardization: Seiri, Seiton, Seiso, Seiketsu and Shitsuke.
- Seiri (Sort) – Eliminating unnecessary items
- Seiton (Set in Order) – Organizing tools and materials for efficiency
- Seiso (Shine) – Keeping the workplace clean and well-maintained
- Seiketsu (Standardize) – Creating consistent procedures
- Shitsuke (Sustain) – Ensuring long-term discipline and improvement
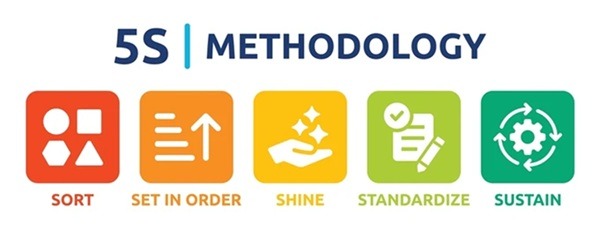
Benefits of Implementing 5S
Implementing the 5S methodology provides numerous advantages that enhance workplace efficiency, safety, and overall productivity. By adopting 5S, organizations can experience the following key benefits:
1. Increased Efficiency and Productivity:
A well-organized workplace ensures that employees spend less time searching for tools, materials, or documents. By eliminating unnecessary items and arranging essential ones in a systematic manner, workflow becomes smoother, and tasks are completed faster. This leads to higher efficiency and improved productivity across all operations.
2. Cost Reduction:
One of the major advantages of 5S is its impact on cost savings. The methodology helps eliminate waste caused by excess inventory, unnecessary movements, and mismanagement of resources. Additionally, by keeping tools and equipment in designated locations, loss and damage are minimized, reducing unnecessary replacement costs.
3. Improved Workplace Safety
A cluttered and disorganized workspace often leads to accidents and injuries. With 5S principles, hazards such as spills, misplaced tools, and obstructed walkways are identified and eliminated. This proactive approach to safety reduces workplace incidents, ensuring a secure environment for employees.
4. Better Quality and Consistency:
Standardizing workplace organization and procedures plays a crucial role in maintaining high-quality output. When workstations are clean, tools are properly maintained, and processes are clearly defined, errors and defects decrease significantly. This results in improved product or service quality and ensures consistency in operations.
5. Enhanced Employee Morale:
A clean and well-organized workplace creates a positive working environment, boosting employee satisfaction and motivation. When employees work in a structured setting with clear expectations, they feel more valued and engaged. Encouraging team participation in 5S activities also fosters a sense of ownership and responsibility.
6. Supports Continuous Improvement (Kaizen):
5S is not a one-time initiative but rather a foundation for ongoing improvements. It aligns with the Kaizen philosophy, where small, continuous enhancements lead to long-term success. By maintaining discipline and sustaining 5S practices, organizations can adapt to changing business needs and drive innovation.
10 Simple Steps for 5S Implementation
Form a 5S Team: To begin the process of implementing 5s, it is important to establish a committed 5S team. This team will lead, coordinate, and execute the entire 5S process. The team should consist of individuals from various departments and levels within the organisation to ensure a comprehensive perspective and smooth implementation. It is essential to have representatives who understand the current workflows, processes, and challenges in different plant areas. The team will also drive the cultural change required for successful 5S implementation.
Executing a Gemba walk: Before diving into the 5S process, conducting an initial plant walkthrough is crucial. This involves performing a Gemba walk, which means going to the actual workspace where the work is being done. The purpose of Gemba is to observe and gather information about the current state of the plant. During the Gemba walk, the 5S team and leaders should engage with employees, ask questions, and gain insights into the existing work environment, practices, and potential improvement areas.
Plant Area Distribution (Zone Wise): Following a Gemba walk, the plant is segmented into various zones according to its design and the nature of tasks carried out in each section. Each zone is then assigned to a particular team member who takes charge of implementing the 5S methodology. Assigning zones to team members helps to clarify responsibilities for maintaining cleanliness and organisation, establish accountability, and promote standardisation.
Sorting Phase (Seiri): The Sorting phase, also known as Seiri, focuses on decluttering and eliminating unnecessary items from the workspace. Team members in each zone identify and separate items essential for the current operations from those no longer needed. Red tags are commonly used in this phase, where items marked with red tags are considered obsolete. After identifying those unnecessary items, the team decides whether to dispose of, relocate, or store them appropriately. The goal is to create a clutter-free and efficient workspace that contains only the necessary tools and materials.
Set In Order Phase (Seiton): In the Set In Order phase, also called Seiton, the goal is to methodically and effectively arrange the items needed for ongoing operations. During this phase, the team determines the best locations for tools, equipment, and materials. Every item is given a specific place, and visual aids like shadow boards, labels, and floor markings indicate where the items should be stored. Such an organisation reduces the time spent searching for tools and enhances overall workplace efficiency.
Shine Phase (Seiso): The Shine phase, or Seiso, involves cleaning and thoroughly maintaining the workspace and equipment. To achieve this, the team should create a regular cleaning schedule that involves everyone in the area. Doing so will not only improve the appearance of the workplace but also help identify potential safety hazards and equipment issues that can be resolved promptly. A clean and organised environment boosts employee morale, improves productivity, and shows a dedication to quality.
Standardise Phase (Seiketsu): The Standardise phase, or Seiketsu, aims to establish standardised processes and practices for 5S across all zones in the plant. The team collaboratively develops guidelines, checklists, and visual standards that clearly define the expectations for each 5S element. Standardisation ensures consistency in implementation, making it easier for employees to follow the 5S principles throughout the organisation. Regular training and communication ensure everyone understands and adheres to the established standards.
Sustain (Shitsuke) Phase: The Sustain phase, or Shitsuke, is the most critical step in the 5S implementation process. It involves creating a culture of continuous improvement and long-term commitment to 5S principles. The 5S team and leaders should work on reinforcing the 5S practices by providing feedback and rewarding employees who actively maintain the 5S standards. Sustaining 5S requires ongoing effort and dedication from all levels of the organisation.
5S Audit: The 5S audit systematically assesses each zone’s adherence to the 5S principles. Audits are typically conducted at regular intervals, and they involve evaluating the condition of the workplace, compliance with standardised procedures, and overall adherence to the 5S methodology. The 5S team and representatives from other departments perform the audit using a predetermined checklist. The audit findings help identify areas that need improvement and provide insights into the effectiveness of the 5S implementation.
Corrective Actions on 5S Points: The final step involves taking corrective actions based on the findings of the 5S audit. Identified issues and opportunities for improvement are addressed promptly. The 5S team works with employees and leaders to implement necessary changes, reinforce training, and refine processes. Continuous improvement is at the core of this step, as the aim is to enhance the 5S practices continually and sustain a clean, organised, and efficient workplace.
Toyota: Implementation of 5S in Service Operations
Case Study
Toyota, known for its Toyota Production System (TPS) and commitment to continuous improvement, applied the 5S methodology in its service operations at the Toyota Dasmarinas-Cavite service center in the Philippines. The service center was facing challenges in managing its workshop, leading to inefficiencies, long waiting times for customers, safety hazards, and poor employee engagement. The company recognized the need for a systematic approach to organize the workplace, improve employee productivity, and enhance overall service quality.
The 5S Methodology: The 5S methodology was applied in the following steps:
Sort (Seiri):
- The first step involved identifying and separating tools, equipment, and materials that were not needed for the current operations.
- Unnecessary items were removed, and the workspace was cleared of clutter.
Set in Order (Seiton):
- All essential tools, equipment, and parts were organized to be easily accessible.
- Tools were placed in designated spots, and color-coded labeling was used to identify items quickly, reducing the time spent looking for tools.
- A visual management system was set up to show where each item should be placed.
Shine (Seiso):
- The service area, including workstations, equipment, and machinery, was thoroughly cleaned.
- Regular cleaning routines were established to ensure the service area remained in optimal condition.
- Workers were encouraged to clean their workspaces as part of their daily routine, promoting a sense of responsibility.
Standardize (Seiketsu):
- Standard operating procedures (SOPs) were established for the use of tools, equipment, and the overall maintenance of cleanliness and order.
- Checklists and schedules for maintenance were created to ensure that 5S practices were consistently followed.
- Visual controls were put in place, including charts and labels to guide workers on how to maintain cleanliness and organization.
Sustain (Shitsuke):
- To sustain the improvements, Toyota introduced a culture of continuous improvement and employee involvement.
- Daily audits were conducted to ensure that 5S practices were maintained.
- Employees were trained regularly, and feedback was gathered to improve the system further.
- Management played an active role in supporting and enforcing the 5S practices.
Implementation:
- Toyota began the 5S implementation by involving employees at all levels, ensuring they understood the benefits and were motivated to participate in the process.
- The company provided training sessions and workshops to educate the staff about the 5S methodology and its importance.
- Tools and materials were standardized, and dedicated storage spaces were created to organize the service area efficiently.
- Managers and team leaders were assigned the responsibility of monitoring the effectiveness of 5S practices, ensuring adherence to the guidelines.
- Regular meetings were held to discuss progress and challenges, and adjustments were made as necessary.
Results: The implementation of 5S at the Toyota Dasmarinas-Cavite service center resulted in the following outcomes:
Improved Workplace Organization:
- The service center experienced a dramatic reduction in clutter, and tools and equipment were much easier to find.
- The workshop became more efficient, with workers spending less time searching for items.
Increased Productivity:
- With a more organized workspace, technicians were able to complete jobs faster, reducing the overall service time for customers.
- The time taken to retrieve tools and parts decreased significantly, improving operational efficiency.
Enhanced Customer Satisfaction:
- The organized and efficient service center allowed Toyota to serve more customers in less time, leading to shorter wait times.
- The improved efficiency translated into a better customer experience, with more customers being satisfied with the service quality.
Improved Safety and Reduced Accidents:
- With a clean and organized work environment, the risk of accidents decreased.
- Proper labeling of items and clear pathways for movement helped eliminate safety hazards.
Employee Engagement and Satisfaction:
- Employees felt more involved in the improvement process, and their sense of ownership in the workplace increased.
- The visual management system empowered workers to take responsibility for maintaining order and cleanliness.
- Staff morale improved as employees noticed the positive impact of 5S on their daily work lives.
Cost Savings:
- With less wasted time and improved workflow, operational costs were reduced.
- The service center was able to handle more customers with the same resources, increasing profitability.
Conclusion
The implementation of the 5S methodology at Toyota’s Dasmarinas-Cavite service center proved to be highly successful. By focusing on workplace organization, cleanliness, and standardization, Toyota was able to enhance operational efficiency, improve customer satisfaction, reduce safety hazards, and increase employee engagement. The company’s commitment to continuous improvement and employee involvement played a crucial role in the success of the 5S initiative. This case study serves as an excellent example of how 5S can be applied outside of traditional manufacturing settings to achieve significant operational improvements.
Moreover, Toyota’s approach included providing Operational Excellence Training Programs for their employees to ensure everyone understood the 5S principles. These programs were designed to foster continuous learning and improvement, helping workers implement 5S successfully in their daily tasks.